Colabora: ÓSCAR AUSÍN, Project Manager del Área Servicios Tecnológicos Avanzados del ITCL
Los centros tecnológicos de diferentes ciudades españolas, coordinados desde la Federación Española de Centros Tecnológicos, han puesto en marcha iniciativas para utilizar las técnicas de impresión en 3D en la fabricación de componentes de mascarillas, pantallas protectoras o tiradores de puertas especiales que evite la propagación del coronavirus. Una forma de poner la tecnología al servicio del bien común.
Allá donde nadie llegaba, las comunidades makers fueron los primeros en reaccionar, y en apenas semanas, se constituyeron y reforzaron diferentes grupos de voluntarios por todo el territorio nacional con un objetivo común: poner las impresoras 3D al servicio de las instituciones sanitarias. En Canal Empresa hablamos con uno de los coordinadores de esta iniciativa en la provincia de Burgos, Óscar Ausín, técnico del Instituto Tecnológico de Castilla y León (Itcl), que asegura que con “una mínima infraestructura”, deslocalizando la fabricación y reduciendo los tiempos de entrega “se ha puesto en relieve el apoyo de una sociedad comprometida con su vecino”.
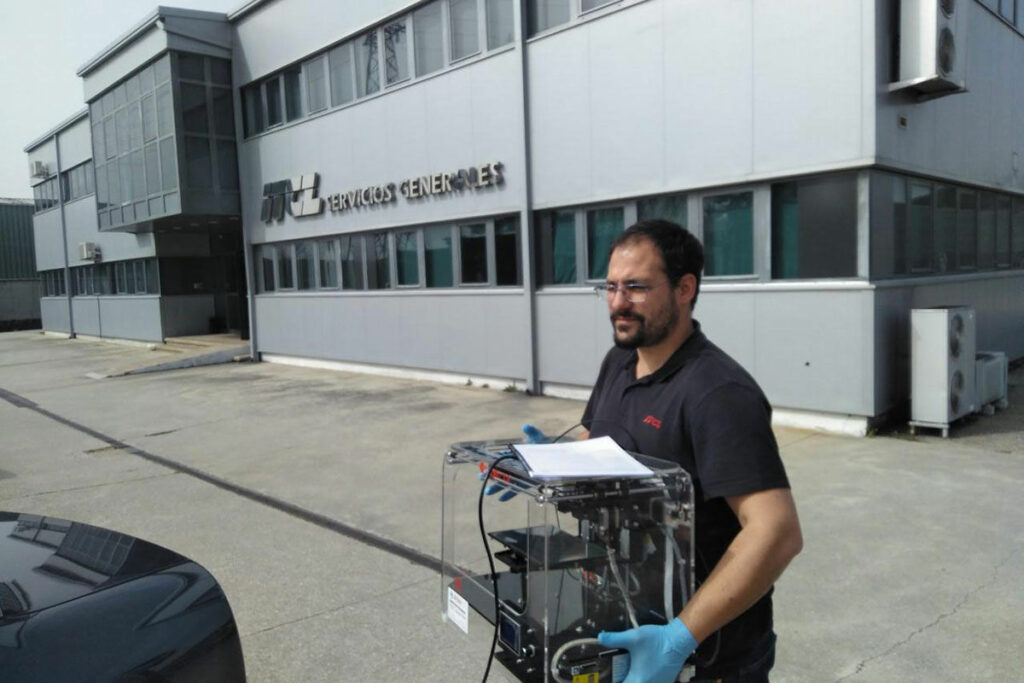
Óscar Ausín trasladando una impresora 3D procedente de Fundación Caja de Burgos.
¿Por qué la tecnología 3D ha salido reforzada tras el coronavirus?
Esta tecnología sale reforzada de esta crisis por su uso en muchos ámbitos con una respuesta y adaptación muy rápida. La sociedad ha podido ver todas las posibilidades de la tecnología fuera del uso industrial o como hobby, viendo que se pueden hacer cosas útiles y necesarias. La fabricación aditiva ha permitido una rápida respuesta frente a otras técnicas de fabricación, permitiendo aliviar el mercado mientras los fabricantes tradicionales construyen sus moldes y comienzan la fabricación de grandes tiradas.
¿Cuál es su potencial en momentos de crisis?
Los mayores potenciales son la fabricación descentralizada, inmediata y cercana a la demanda, el bajo tiempo de respuesta y un alto aprovechamiento del material disponible, que puede ser crítico en momentos de crisis.
Una respuesta muy rápida, para hacerse una idea las primeras versiones de las pantallas protectoras estaban saliendo el pasado 13 de marzo. La comunidad Maker de Burgos ha fabricado en estos días más de 22.000 pantallas de protección con más de 30 versiones del modelo original.
¿En cuánto tiempo se hace una visera de protección?
Con los últimos modelos optimizados para impresión 3D, se puede fabricar una pantalla en menos de 30 minutos o tardar 4 horas en diseños más complejos.
¿La impresión 3D abarata los costes?
Tradicionalmente los prototipos se tenían que fabricar en arcillas, fibra de vidrio o por mecanizado, lo que implica un gran coste por cada versión de prototipo, tanto económico, como en horas de personal técnico.
Sin embargo, la impresión 3D permite hacer correcciones continuas de los diseños de forma muy rápida, sin elevados costes, ya que no requiere la fabricación de ningún molde, lo que permite adaptar los diseños continuamente con los feedback de los destinatarios.
En resumen, en poco tiempo podemos tener una pieza funcional sobre la que poder realizar pequeños ajustes antes de enviar a fabricar los costosos moldes de inyección para largas tiradas.
¿Qué conocimientos se requieren para utilizar una impresora 3D?
Hay máquinas de todo tipo, algunas son como una “cafetera”: las sacas de la caja, la enchufas y en dos minutos está imprimiendo, incluso enviando desde nuestro móvil el diseño a imprimir a través de una APP. Este tipo de máquinas no requieren conocimientos para su uso. Tenemos gente en la comunidad Maker de Burgos de todos los ámbitos, algunos de ellos se han comprado la máquina en estos días y en un par de horas, estaban fabricando pantallas. También se han unido a la iniciativa empresas de todos los sectores que ya usaban esta tecnología en sus procesos, y diseñadores que han hecho que los modelos evolucionasen muy rápido.
Tras el coronavirus, ¿habrá una mayor apuesta de esta tecnología en la fabricación industrial o afectará más a nivel particular?
En la industria tradicional ya se estaba integrando, en su gran mayoría en los procesos de prototipado, utilería, elementos de mantenimiento y control de calidad. Por otra parte, ya hay industria incluyendo elemento fabricados con esta tecnología en su producto y fabricando la pieza final para cliente.
La gran variedad de materiales te permite “imprimir” en plásticos, metales, resinas, cerámicas…. Algunos de estos materiales con certificación para uso médico.
Esta tecnología permite fabricar piezas que, por los sistemas tradicionales, serían imposibles. Por ejemplo, podemos obtener piezas mucho más ligeras, con la misma o mayor resistencia, ya que no consiste en quitar material a un bloque, si no, en aportar material solo donde hace falta, lo que permite hacer vaciados en ciertas zonas inaccesibles por la maquinaria tradicional.
Esta tecnología tiene más de 35 años, aunque en los últimos 6 años, gracias a su abaratamiento es cuando ha permitido que cualquier persona pueda utilizarla en su casa.
Por 300€ tienes una máquina que te permite hacer muchas cosas. Cuando empezamos con esta tecnología, había solo un par de materiales con los que fabricar las piezas, a día de hoy hay cientos, y cada día surgen más.
¿Qué ha puesto de relieve la actuación de los makers en la provincia de Burgos?
La situación actual de la comunidad maker ha permitido una rápida organización con una mínima infraestructura, deslocalizando la fabricación, reduciendo los tiempos de entrega y ha puesto en relieve el apoyo de una sociedad comprometida con su vecino y con la capacidad de ayudar sin exponerse al contagio. Esto ha sido posible a nivel local por una comunidad que ya estaba conectada y unida antes de la crisis, que compartía experiencias y conocimientos en entornos como la FabLab y en eventos multitudinarios que hemos visto pasar estos últimos años sin mucha publicidad ni repercusión mediática.
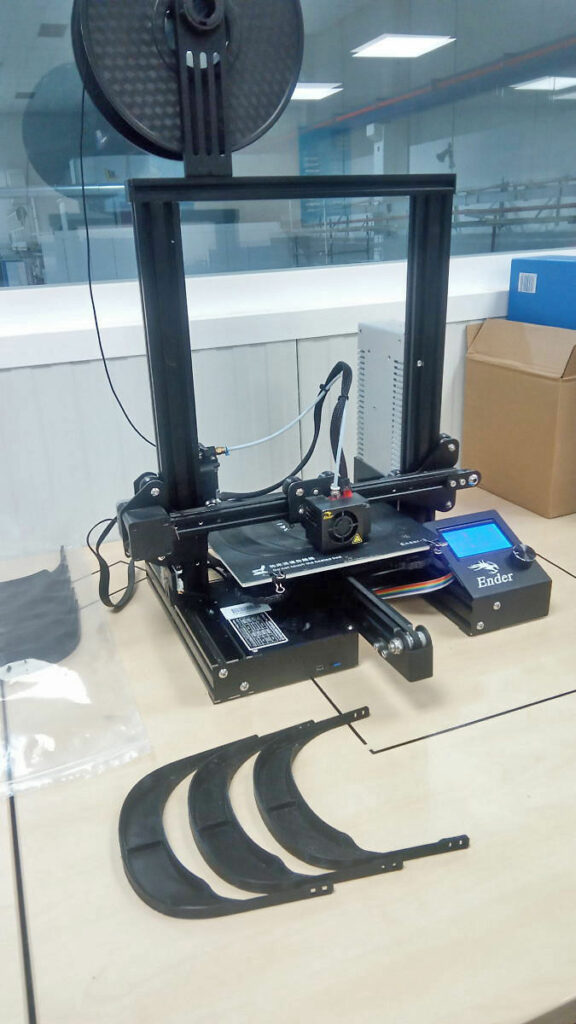
Impresora cedida por el programa educativo Bebot al grupo maker de Miranda de Ebro.